Mill River Runs Through It
Sustainability
An annual effort helps keep Paradise Pond thriving
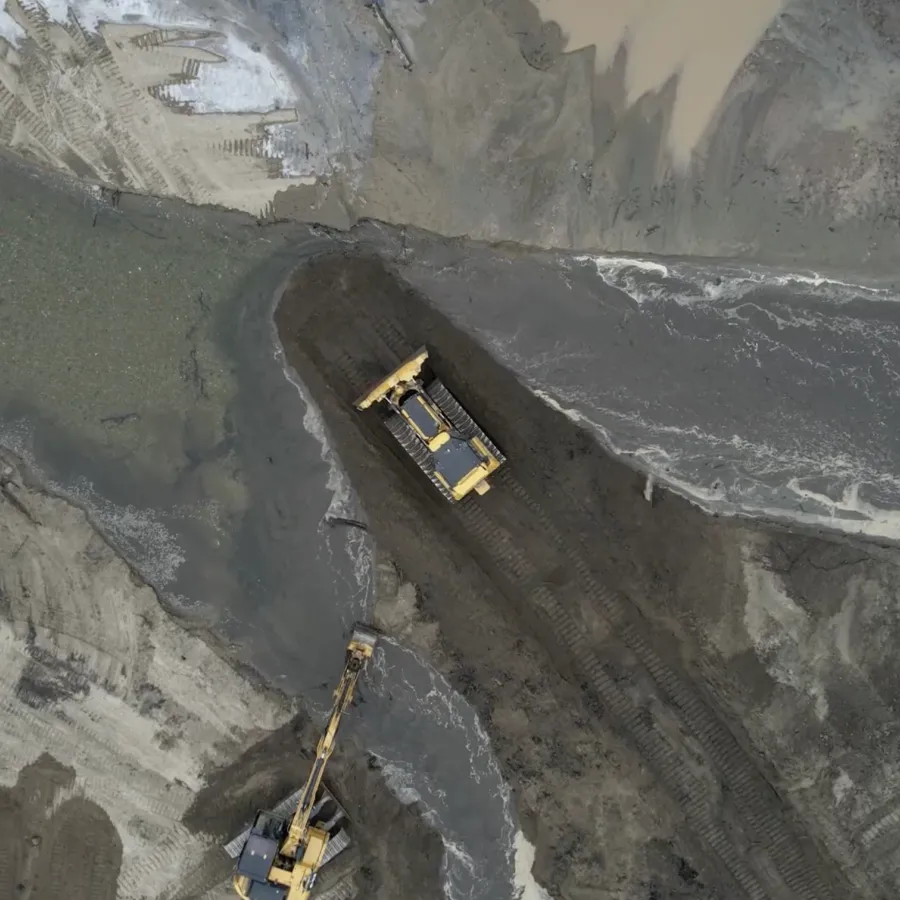
Drone footage by Kala'i Ellis and the Spatial Analysis Lab
Published February 29, 2024
From the start of early December, the bed of Paradise Pond has been sandy and bare. A turbid river made quick work of carving a deep gully in the soft earth. Sometimes excavators and bulldozers worked the ground while a drone buzzed overhead. What was wrong with Paradise Pond?
In a word: Nothing.
The winter drawdown—a period when the pond is deliberately emptied of water—is part of an ongoing strategy to use the natural power of the river to keep the pond from being filled in by sediment, including silt, leaves, and sticks.
Begun as an annual effort five years ago and evolving each year, the drawdown, or more officially the “Paradise Pond Sediment Redistribution” effort, is carefully monitored work (complete with all the regulatory permits) and a highly managed process—as much as any effort can be when relying on a natural system to cooperate.
This year, efforts were hampered by a few extreme weather events, including a December 17 storm that refilled the pond with sand and debris just as efforts to move the buildup downstream were getting underway.
Such efforts are necessary to maintain Paradise Pond, which is an artificial water feature. The pond traces its origins back to the late 1600s, when a dam was first constructed on the site to harness the river, notes Robert Newton, professor emeritus in the department of geosciences, who has been working with the pond efforts for several decades.
“There’s been a pond here for a very long time,” he said. “It’s a great place for building a dam and having water power.”
With the Mill River drawing from 55 square miles of drainage basin upstream and emptying into roughly nine acres of pond area, even unexceptional years of water flow bring enough silt, sand, rocks, sticks, and trees to gradually fill up the small pond basin.
To maintain the campus feature, the college long relied on a “dredge and haul” model. Every eight years, the pond would be emptied of water, dried out, and excavated over a three-week period. The excess sand and gravel was then trucked to a landfill, where the disposal costs in 1998—the last time the process was done—were upwards of $9 per cubic yard. (Similar "tipping fees" today could cost roughly $31.50 per cubic yard.) Adding up the dry excavation, tipping fees, engineering, and miscellaneous work, the college spent $533,000 that year on the pond project.
In 2008, the college experimented with hydraulic excavation, using a barge and special equipment to suction up the pond bottom before it was dried out and hauled away. This effort, originally designed as a summer project, took over six months and cost approximately $700,000 to remove 12,800 cubic yards of material. Then there was the problem of what to do with the sediment once it was removed.
“As time went on and the regulations became stricter, there were fewer and fewer places you could haul it to,” said Newton. “If you can’t drain it and you can’t take the soil anywhere, what are you going to do?”
By 2013, as permitting for the next round of dredging was in process, state and federal regulators asked if the college would consider flushing sediment downstream, an option that had previously been prohibited. The new option completely changed Smith’s approach, noted facilities management project manager Gary Hartwell, who has overseen the pond efforts for almost 30 years.
“We understood what that meant immediately,” he said.
Several years of experimentation followed, including attempts to simply open a sluice gate located at the Paradise Pond dam (“did almost nothing”), partial draw-downs of pond water levels, and “dosing” the river by using a bulldozer to push material into the natural flow of the river. The latter effort worked well enough, although it removed only 2,000 cubic meters of sediment.
Three years ago, Hartwell and Newton came up with a plan to redirect the Mill River by carving a narrow channel in the pond bed. By creating a new path each year, they are now able to harness the river’s ability to quickly sculpt out and carry away the silt. The new process, which legally must take place between November 1 and April 1, now removes between 3–5,000 cubic yards of sediment per year and costs less than $30,000 for equipment usage.
“It’s way cheaper,” said Hartwell, “but the real advantage is the sediment stays inside the system.”
Every stage of the process is carefully monitored, from water flow and temperature to channel erosion. There are even ongoing studies of the impact to individual mussels living below the dam. Aerial photography using drone flights helps map the pond before and after each effort, down to the centimeter.
“What we really want to get to is a balance of monitoring how much comes in and making sure that much goes out,” said Hartwell. “What if the dam weren't there, what would the river do?”
Following a successful attempt to move sediment this February, Hartwell anticipated that the pond would start refilling with rain and return to its higher water levels by the start of March.
Tula Economou ’85 learned about the project from Newton, her former professor, while on a recent visit to the campus. As the vice president and division manager at Apex Environmental Engineering, where she oversees similar efforts, Economou declared the Smith project a “win-win-win.”
“I just feel like this is such an interesting and well-thought out solution,” she said. “It’s such a much more tangible and important way to serve the alums and the students of the college than to unnecessarily spend money dredging a pond.”